Plastic extrusion for pipes, sections, and custom shapes
Plastic extrusion for pipes, sections, and custom shapes
Blog Article
Comprehending the Essentials and Applications of Plastic Extrusion in Modern Manufacturing
In the world of modern-day manufacturing, the strategy of plastic extrusion plays a critical function - plastic extrusion. This intricate procedure, entailing the melting and shaping of plastic through specialized dies, is leveraged across numerous markets for the production of diverse items. From automobile parts to durable goods packaging, the applications are substantial, and the potential for sustainability is similarly impressive. Unwinding the principles of this procedure reveals real versatility and capacity of plastic extrusion.
The Principles of Plastic Extrusion Process
While it may appear complicated, the basics of the plastic extrusion process are based on fairly simple principles. It is a manufacturing process in which plastic is melted and after that formed into a continual account through a die. The raw plastic product, commonly in the type of pellets, is fed right into an extruder. Inside the extruder, the plastic undergoes warm and pressure, creating it to melt. The molten plastic is then required with a shaped opening, understood as a die, to form a long, constant item. The extruded item is cooled down and after that reduced to the preferred size. The plastic extrusion procedure is thoroughly made use of in numerous markets because of its adaptability, effectiveness, and cost-effectiveness.
Different Kinds of Plastic Extrusion Techniques
Structure upon the basic understanding of the plastic extrusion procedure, it is necessary to check out the numerous methods entailed in this manufacturing approach. The two main strategies are profile extrusion and sheet extrusion. In account extrusion, plastic is thawed and formed into a continual account, frequently made use of to create pipelines, poles, rails, and window frames. On the other hand, sheet extrusion creates huge, level sheets of plastic, which are generally additional refined into items such as food packaging, shower drapes, and automobile components. Each technique needs specialized equipment and exact control over temperature and pressure to guarantee the plastic keeps its form throughout air conditioning. Recognizing these strategies is key to utilizing plastic extrusion successfully in modern-day production.
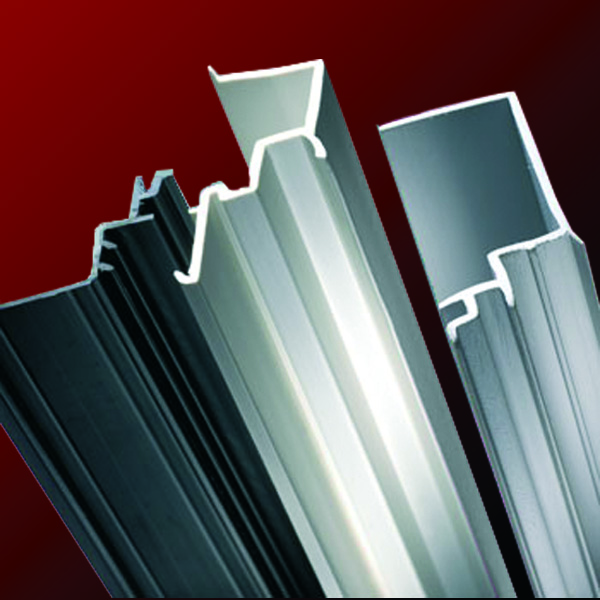
The Function of Plastic Extrusion in the Automotive Industry
An overwhelming bulk of components in contemporary automobiles are products of the plastic extrusion process. This procedure has revolutionized the auto market, transforming it right into a more reliable, economical, and flexible production industry. Plastic extrusion is largely utilized in the production of various car components such as bumpers, grills, door panels, and control panel trim. The process supplies an uniform, constant result, allowing manufacturers to create high-volume get rid of excellent precision and minimal waste. The agility of the extruded plastic parts adds to the total reduction in automobile weight, improving fuel performance. The durability and resistance of these parts to warm, cool, and impact boost the durability of cars. Thus, plastic extrusion plays an essential role in auto production.

Applications of Plastic Extrusion in Durable Goods Production
Past its considerable effect on the vehicle market, plastic extrusion shows Visit This Link equally effective in the realm of customer items making. This process is vital in producing a broad range of products, from food product packaging to family home appliances, toys, and also clinical tools. The flexibility of plastic extrusion allows producers to make and create complex forms and sizes with high accuracy and performance. Due to the recyclability of lots of plastics, extruded components can be recycled, decreasing waste and price (plastic extrusion). The versatility, adaptability, and cost-effectiveness of plastic extrusion make it a recommended option for many durable see this site goods suppliers, contributing considerably to the market's growth and technology. The environmental ramifications of this widespread usage need careful consideration, a subject to be gone over even more in the subsequent area.
Environmental Impact and Sustainability in Plastic Extrusion
The prevalent use of plastic extrusion in manufacturing invites scrutiny of its environmental implications. Effective machinery reduces energy usage, while waste management systems reuse scrap plastic, decreasing raw material needs. Despite these enhancements, additionally development is required to alleviate the ecological impact of plastic extrusion.
Conclusion
In conclusion, plastic extrusion plays a crucial duty in modern-day production, especially in the automotive and durable goods sectors. Its adaptability enables the production of a large range of components with high precision. Its possibility for reusing and growth of biodegradable materials provides an appealing method in the direction of lasting techniques, thereby addressing review environmental concerns. Understanding the basics of this procedure is vital to maximizing its advantages and applications.
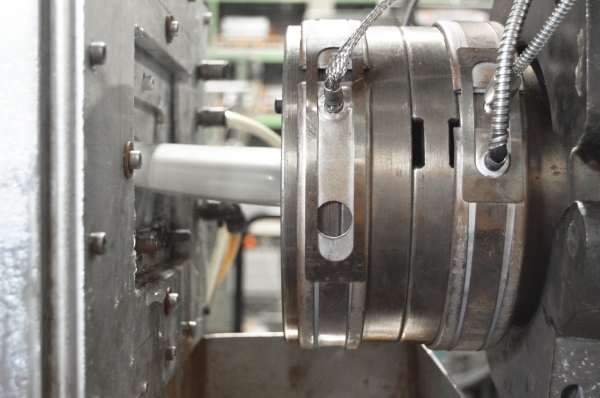
The plastic extrusion process is extensively made use of in different industries due to its cost-effectiveness, performance, and convenience.
Building upon the basic understanding of the plastic extrusion procedure, it is needed to check out the various strategies entailed in this manufacturing method. plastic extrusion. In comparison, sheet extrusion produces large, level sheets of plastic, which are usually additional refined into products such as food product packaging, shower curtains, and auto components.An overwhelming bulk of parts in modern-day automobiles are products of the plastic extrusion process
Report this page